3D Laser Scanning Technologies for Shipyards
3D laser scanners allow to measure the position of hundreds of thousands points at very high speeds and with millimetre accuracy detecting and defining very large and complex surfaces. These characteristics make it a fundamental aid for the phases of design, construction and installation in shipbuilding.
3D Laser Scanning Technologies in Marine Shipbuilding
3D laser scanning technology is a direct measurement system based on the principle of optical triangulation: projecting a measuring laser line it can detect the profile or size of any surface. Part of the reflected light is captured by the Complementary Metal-Oxide Semiconductor (CMOS) matrix sensor integrated detector and can calculate the distance along the z-axis and the exact position along the x-axis. This instrument is among the most performing for measuring speed and accuracy because, without contact, it can detect, measure, and evaluate objects even in motion.
The result of the acquisition made through a 3D laser scanner is a cloud of points, a very dense set of points that replicates the detected object identically.
The answers obtained by this laser technology allow to generate NURBS geometries (Non-uniform Rational B-Splines), mathematical representations of 3D geometry that are integrated and processed in CAD or calculation software.
Thanks to NURBS geometries, any curve and surface can be precisely and flexibly created and defined: they have the advantage of requiring less information than is necessary for the representation through polygonal meshes and are a fundamental aid for the phases of design, construction and installation in shipbuilding.
They are commonly used in CAD (Computer Aided Design), in CAM (Computer Aided Manufacturing) and in CAE (Computer Aided Engineering), but also have a standard use in many industrial protocols such as IGES, STEP, ACIS and PHIGS.
Precision for Luxury Yacht Design
Precision and accuracy are two key words of this technology, looming even before the actual laser scanning.
Setting the speed and step parameters of the rotations determines the resolution and quality of the data acquired: the density of the grid of detected points and the quality of the information acquired increase for slower rotations thus determining the duration of the scan that can vary from a few seconds to a few hours.
During the acquisition, the 3D laser scanner stores for each detected point the distance and the horizontal and vertical angles calculated based on the position of the body and mirror, in addition to the reflectance value of the surface affected by the laser which will be as high as this will tend to the white colour. Every phase of this process allows to capture even the smallest detail removing from the equation the subjective interpretation of the spaces from which expensive tolerances are achieved, even in terms of design.
The precision of this technology is vital for the design of luxury yachts. Being able to have such accuracy allows to dispose spaces with certainty, both from a logistical and design point of view, both from a design and furniture point of view.
Optimization of Construction Processes
The use of 3D scans allows shipyards to optimize construction processes allowing to verify the congruence between what has been designed and what has been made or, conversely, to start designing that has already been realized.
In this way a shipyard can easily identify and resolve any critical issues between two moulds for fiberglass that must be coupled together but are physically located in different places. A furniture factory instead, can scan and digitize the areas to furnish and design all the furniture and accessories necessary for the interior design with the certainty that what is being realized will be perfectly installable on board, without any unknowns or costly corrections.
Shipbuilding, being still a sector with a predominantly artisanal character, has therefore found in the 3D scanner a valid and multipurpose tool that, properly used, allows to optimize many processes avoiding errors or identifying them in time for intervene.
Repair, Playback and Reverse Engineering
The use of 3D laser scanning technology throughout the industry is also a fundamental support for maintenance and restoration. The accuracy and completeness of the information it produces, efficiency and reduced costs distinguish laser scanning technology from any other relevant methodology. Its characteristics enable the measurement and the complete mapping of structures, plant layouts and piping lines but also census in industrial surveys even in operation or in dangerous conditions.
For the marine industry, the accuracy of the laser survey provides the precise verification of alignments of changes made in repair or replacements’ cases of a part of a boat, the exact reproduction and duplication of a vessel or part thereof, until its use for reverse engineering.
Being able to detect in detail and in three dimensions, 3D laser scanning digitizes a physical object and provides technicians with a database of 3D coordinates accurate to the millimetre for the construction or integration of future new structures, or plant parts’ reconstruction. From this database it is possible at any time extract plants and sections, create 3D models, verify the built and produce tolerance analysis.
The Future of 3D Laser Scanning technologies in the Marine Industry
As with any technology industry, there are continuous developments in technology in 3D scanners’ field that can dramatically enhance the scanning experience.
In particular, trying to significantly reduce the scanning time, or to greatly simplify the alignment procedure between different scans, and in some cases (GeoSLAM) to enable motion scans performed with accuracy comparable to static scans.
At the same time the research works both on the scans’ accuracy and noise reduction, both on user interfaces that allow goodness and accuracy’s perception in real time scansion.
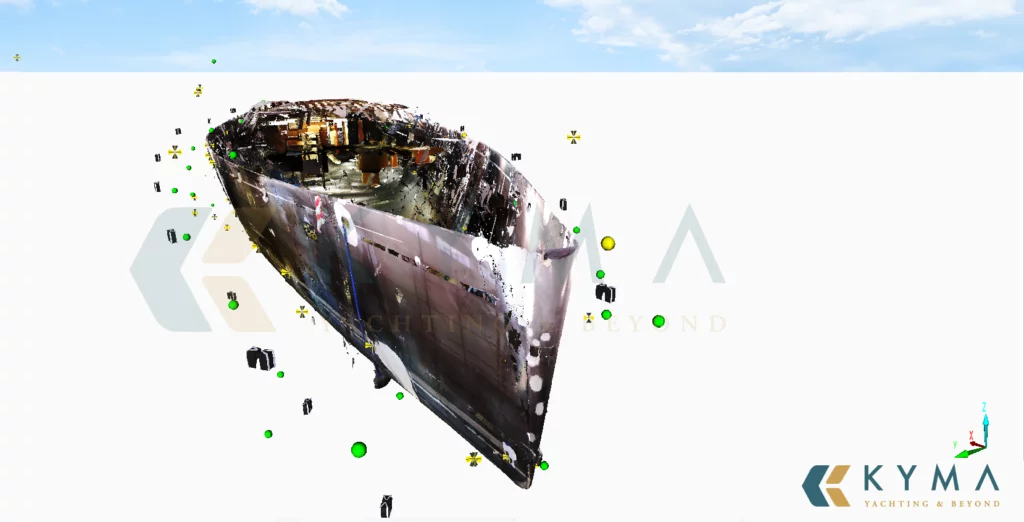
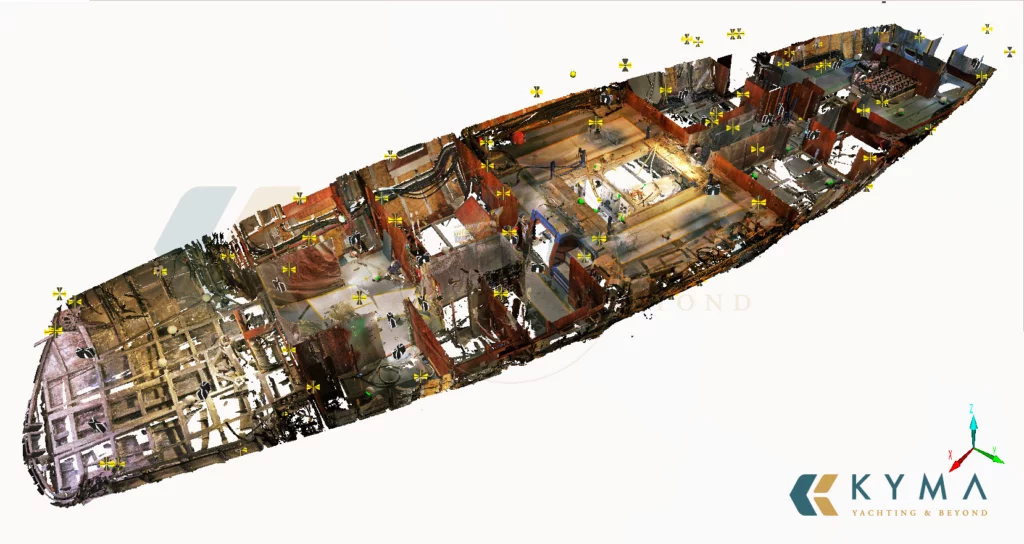
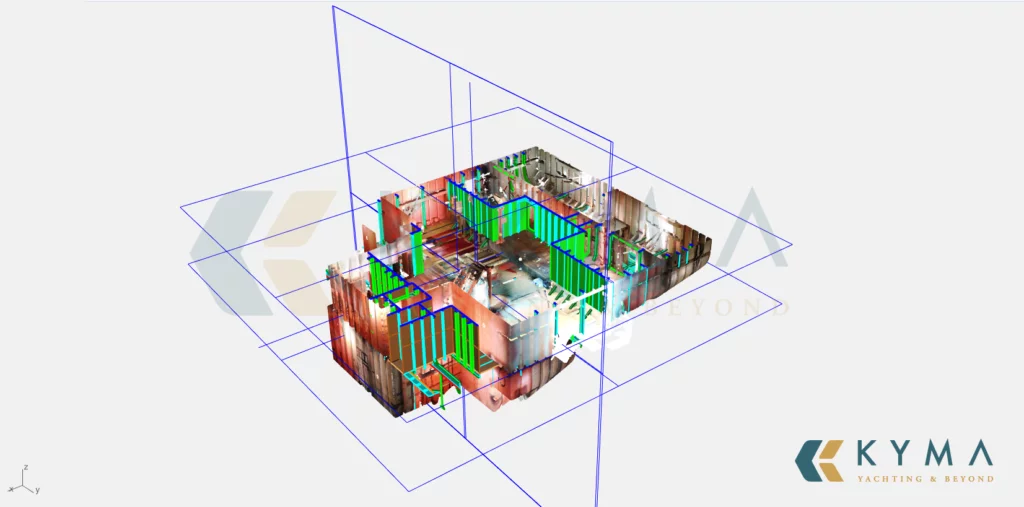

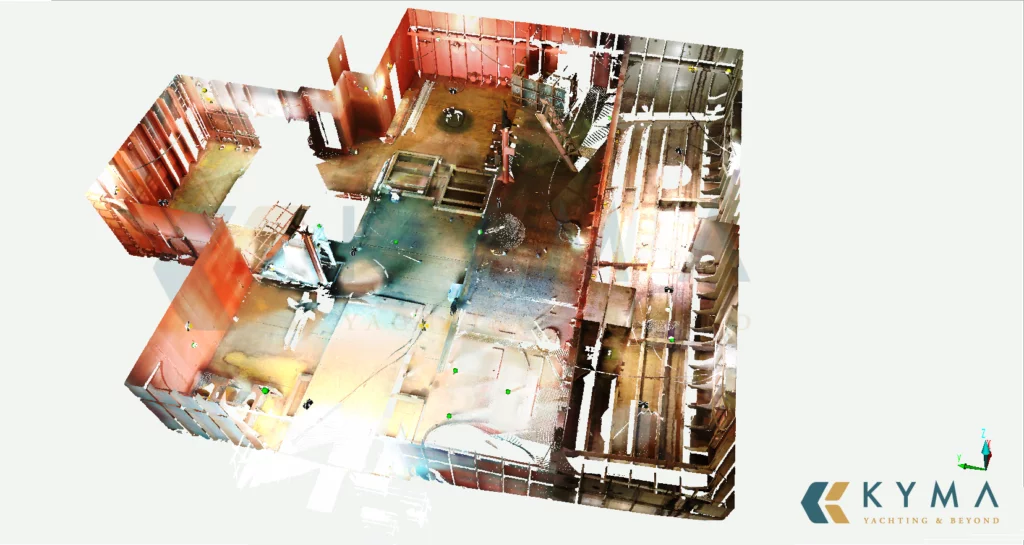
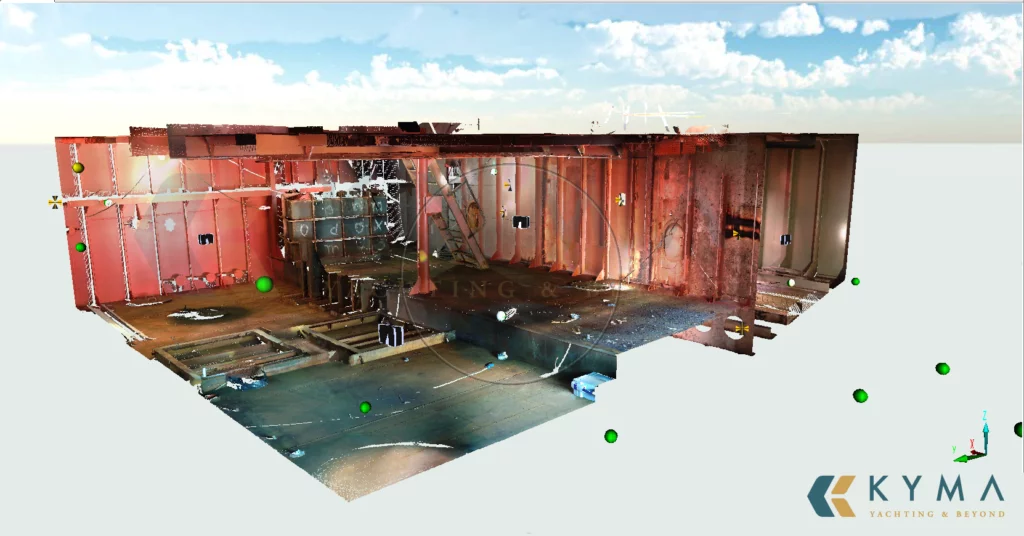
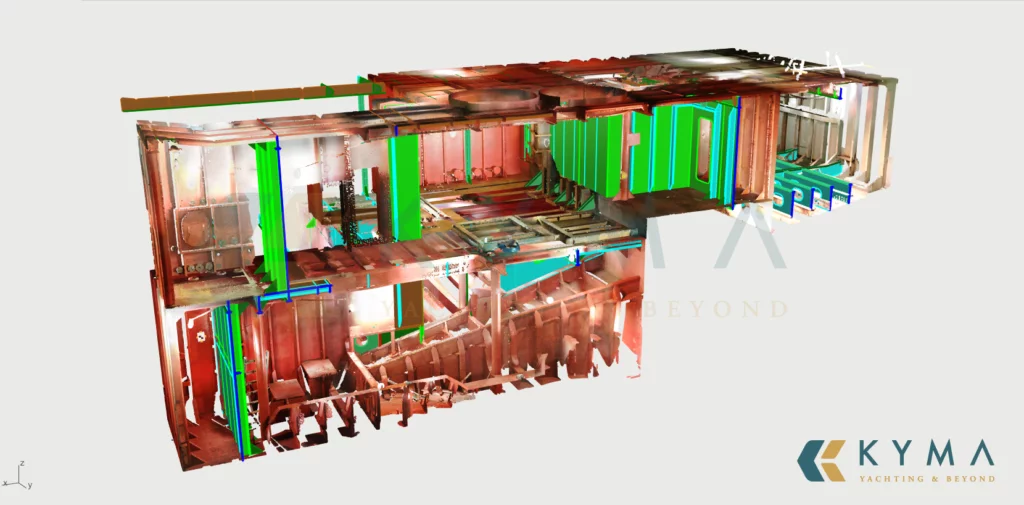

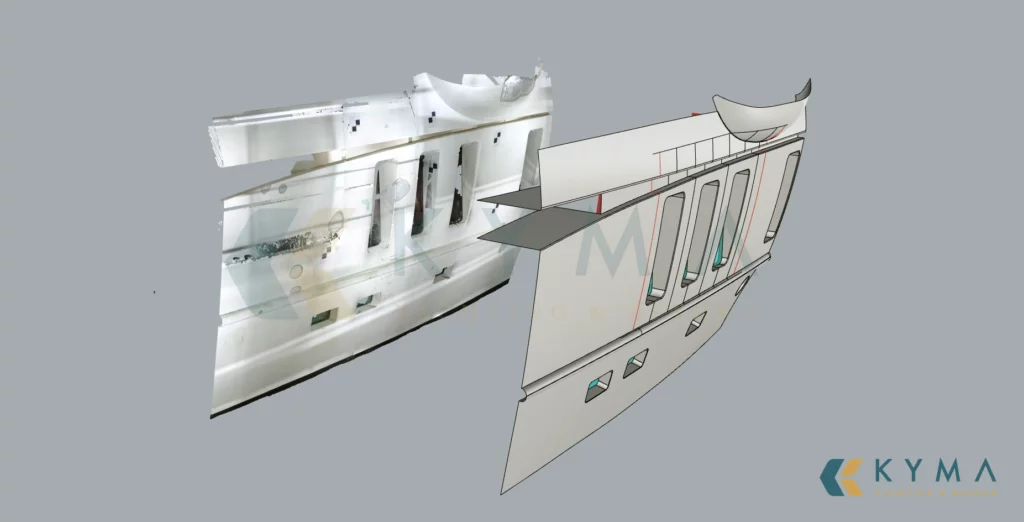
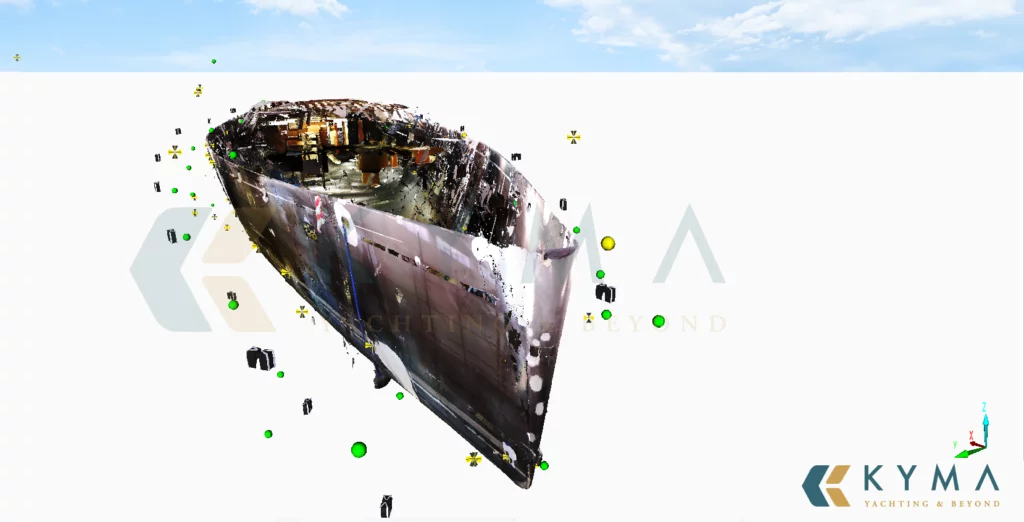
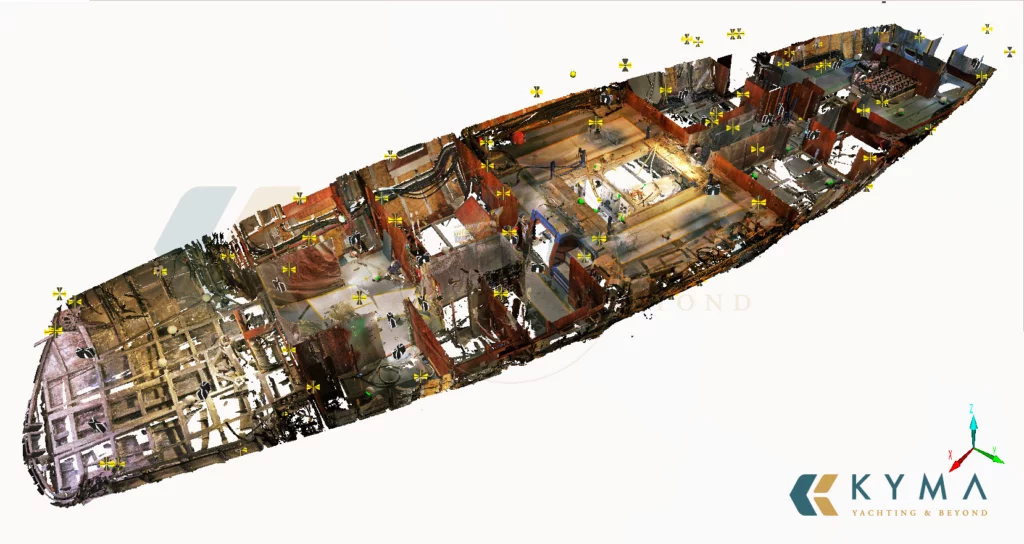
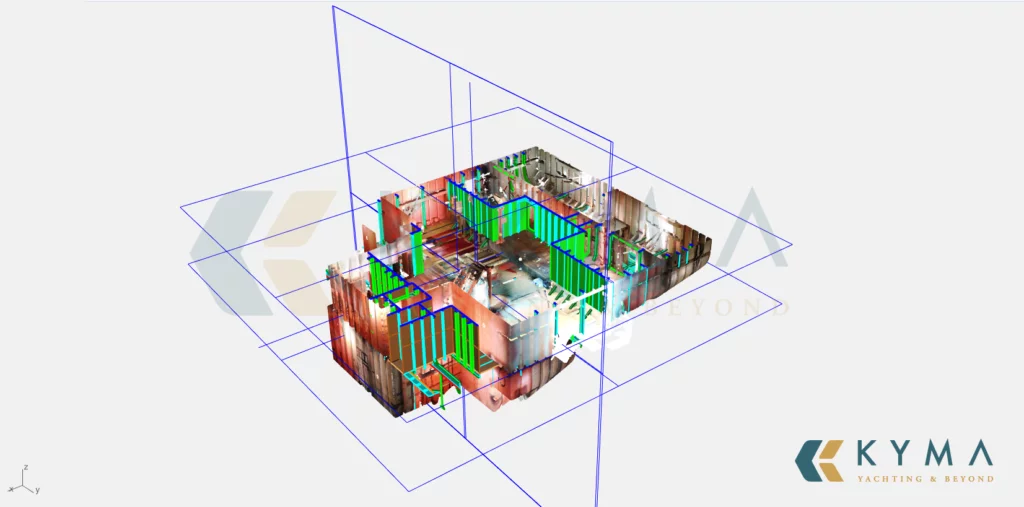

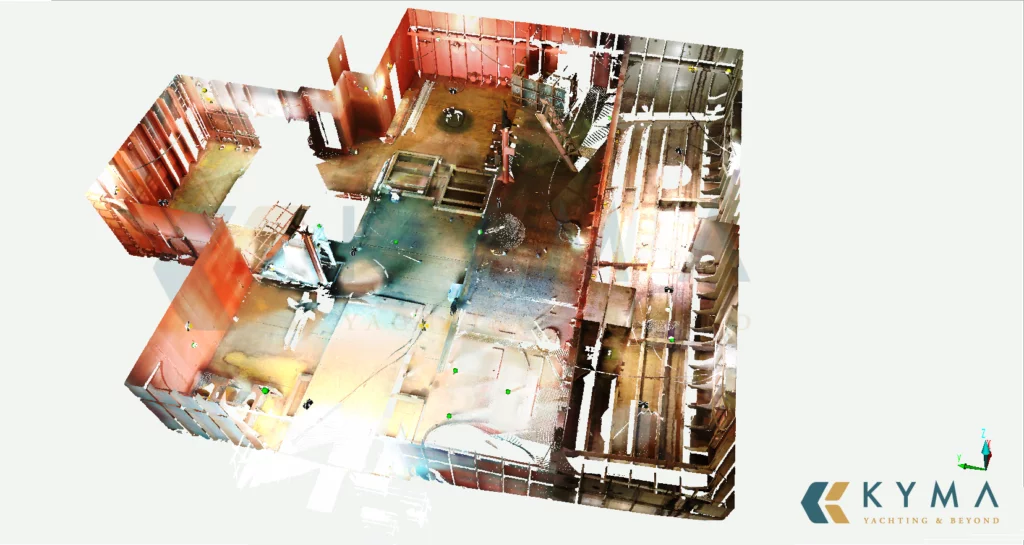
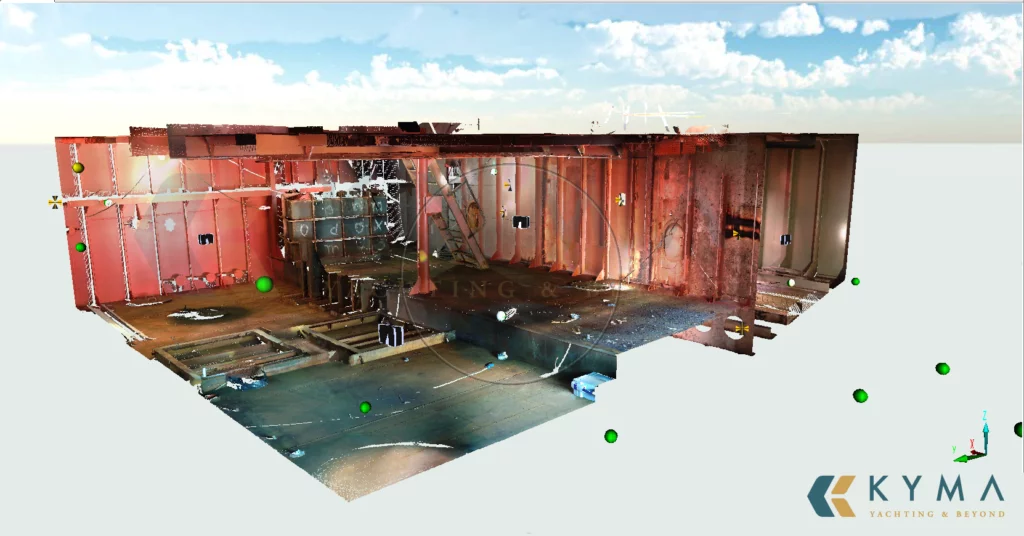
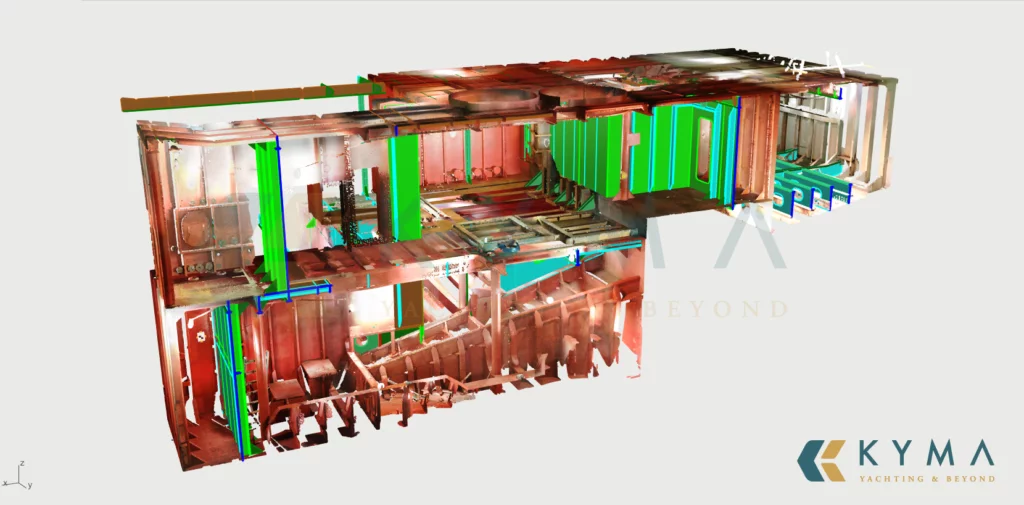

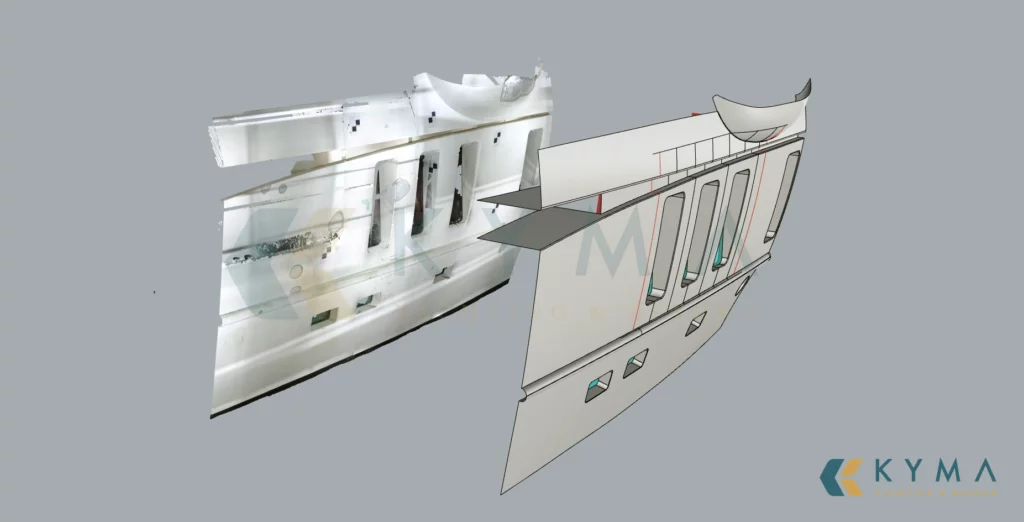