The Importance of a Well-Balanced Design for Piping of Yachts at the Limit of 500GT
The 500GT Limit
In the yachtbuilding industry, exceeding the limit of 500GT in volume means a substantial increase in regulatory requirements and on-board installations that no longer justify the type of product made, due to the higher cost of construction and management resulting from it.
In these cases, i.e., with yacht up to 40 to 50 m in length, the trend among shipyards and designers remains to maximize the space available for customers. To achieve this result are used many measures, that over time have standardized enough to be used each time in different combinations.
Tonnage Limits and Piping
Focusing the attention on the routing of the piping of the on-board systems, some of these solutions have no particular direct effects (for example, reducing the hull width or varying the hull shapes may have implications on stability and performance but in this deepening may be overlooked).
Among the solutions with a strong impact for designing of the on-board routings instead, it’s useful to report at least three:
- The structural deck to deck spacing are lowered as much as possible, while maintaining the net height in the accommodations. Since the structures cannot be reduced as a result, this means less space above the ceiling for the routes of the lines.
- Some areas are excluded from the tonnage’s calculation, leaving them opened as an external space or structurally closed and making them inaccessible. In this case, the space available for machines and switchboards is reduced.
- Finally, as a consequence of the above, in the general arrangements the technical spaces are less and less, increasingly smaller and often of not straight shapes, due to the interface between the external shape and the interior spaces.
Problems and Solutions
Faced with this need, justified by commercial and economic reasons, the challenges for technical designers and installers are increasing. If the issue isn’t managed with attention from the first phases, results inevitably a total quality’s decrease, understood also like operativity’s difficulty and maintenance throughout the life of the vessel.
Referring to plans routing, the first and most immediate response is completely internal and consists in numerous precautions and verifications carried out by the designer himself including:
- a careful choice of line paths to avoid unnecessary crossings and routes as much as possible;
- the identification of the points of penetrations to decks and bulkheads closer to the users to reach;
- efficient organisation of main longitudinal routes.
A “Well-Balanced” Design
But the modeler’s experience and skill alone, however, cannot be enough to solve all the problems. In the nautical design all the main items (interior, structures, outfitting, plants) have objective space needs that cannot be questioned, and, for this reason, they must be studied together so that the result will be as balanced as possible.
In this context we can call a project as “well-balanced” when all the above items are studied together so that, sacrificing each a part of the space that would initially require, we arrive at a final achievement as balanced as possible.
Each yacht is different and a challenge in its own right, so it is not possible to propose a universally valid formula or a manual to follow. The best end result is obtained through the experience that leads to recognize and manage the various problems when it is still possible to remedy or at least limit the impact.
An Interdisciplinary Approach to the Problem
Here are some measures to be studied and implemented from the early stages of the project to facilitate the piping’ design.
- The structural layout must maximize the spaces for the main longitudinal routes and for the transverse crossings, paying particular attention to the relative heights between beams and girders and the holes alignment.
- The interior’s technical items must be carefully defined by designers: the fancoil’s and air plenum position, the space for electrical panels, the alignment of partition bulkheads among different decks. This doesn’t mean deciding the furniture instead of the interior architect, because the designer’s task is defining the furniture and place constraints, choosing between equivalent solutions that can support a better overall result.
- Pay attention to the galley’s layout and its location in the general arrangement. The extraction ducts from the hoods and their natural balancing are bulky and must be kept isolated for fire safety reasons, so care must be taken to ensure their path to external grilles (in turn must be properly placed to prevent odour returns).
- The portion of the superstructure that contains the lobbies is always critical because of the stair trunks and the eventually lift are obstacles to the longitudinal routes of the plants. In this case, the functional diagrams should be designed in such a way as to minimise passages in these areas, in particular for air ducts and cable trays.
- The insulation details shall be made in a way as to minimise the thicknesses at the points where could be more space problems. This process is facilitated by the fact that under 500 GT there are no main vertical zones and other constraints required for bigger vessels. In any case, and especially in critical areas that might occur during work, a certain use’s flexibility is required with the possibility of choosing more performing materials (i.e., thinner with the same insulation performance) but also more expensive.
Kyma: a Vision that Aims at the Final Result’s Quality
At Kyma, great care has always been given to the quality of the final result of commissioned works.
The above analysis is an example of the attention required daily to achieve this standard and is the result of the experience accumulated in over 20 years of shared activity among all the team’s members.
And it’s precisely this experience that Kyma collects and values in the perspective of a continuous improvement of its performance and services, to provide its clients with the highest possible level of quality and efficiency.
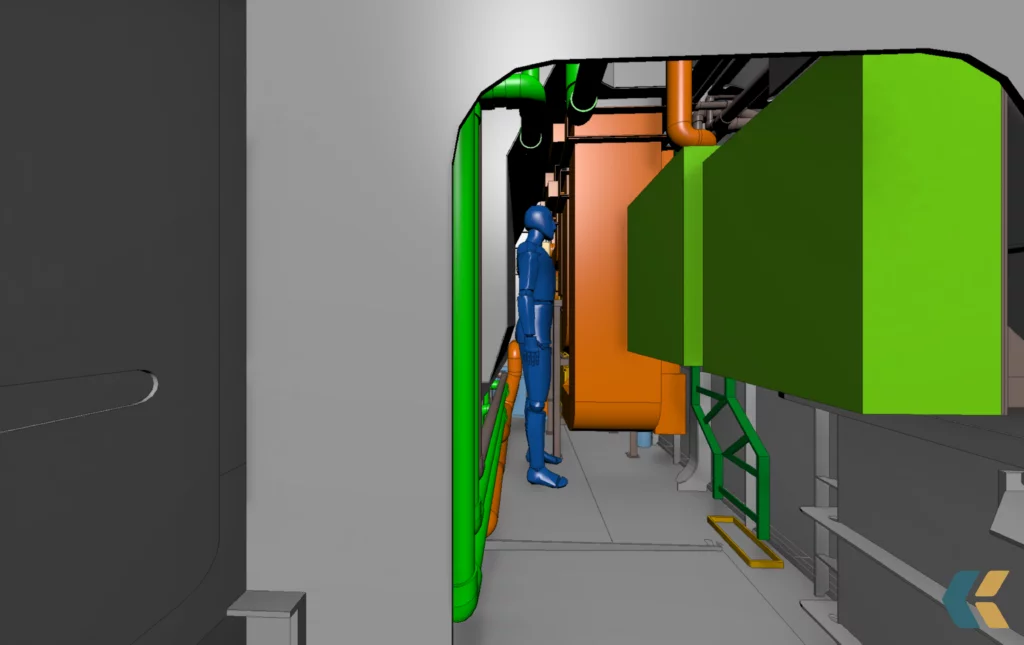
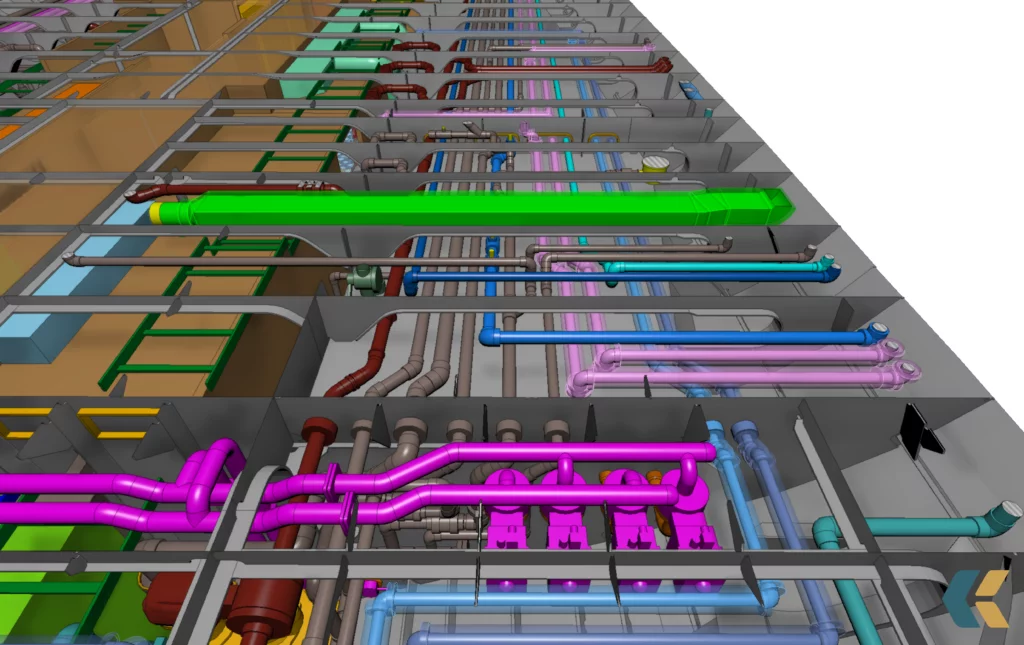
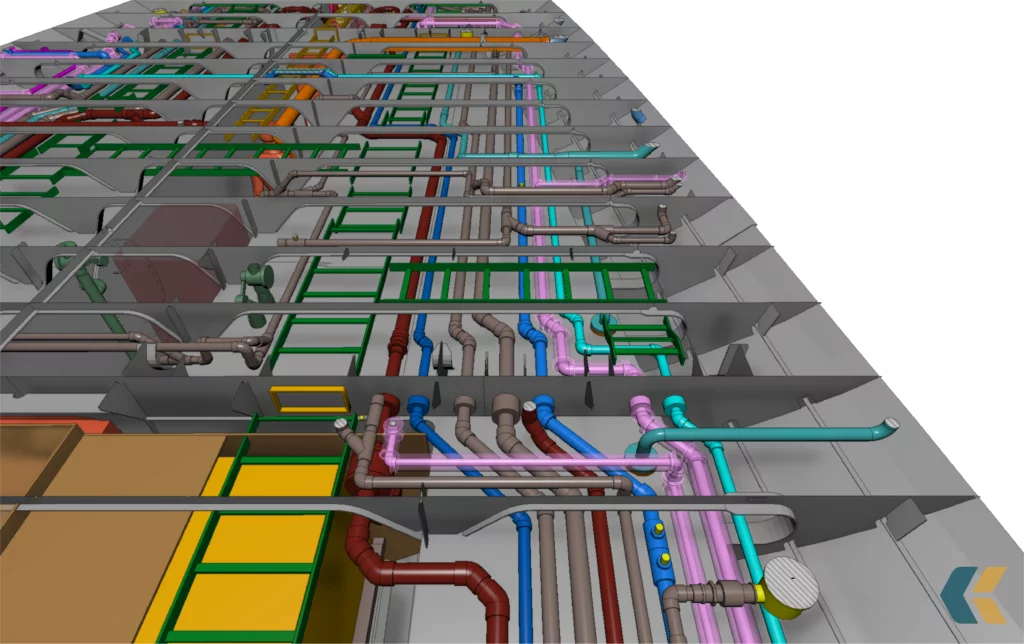
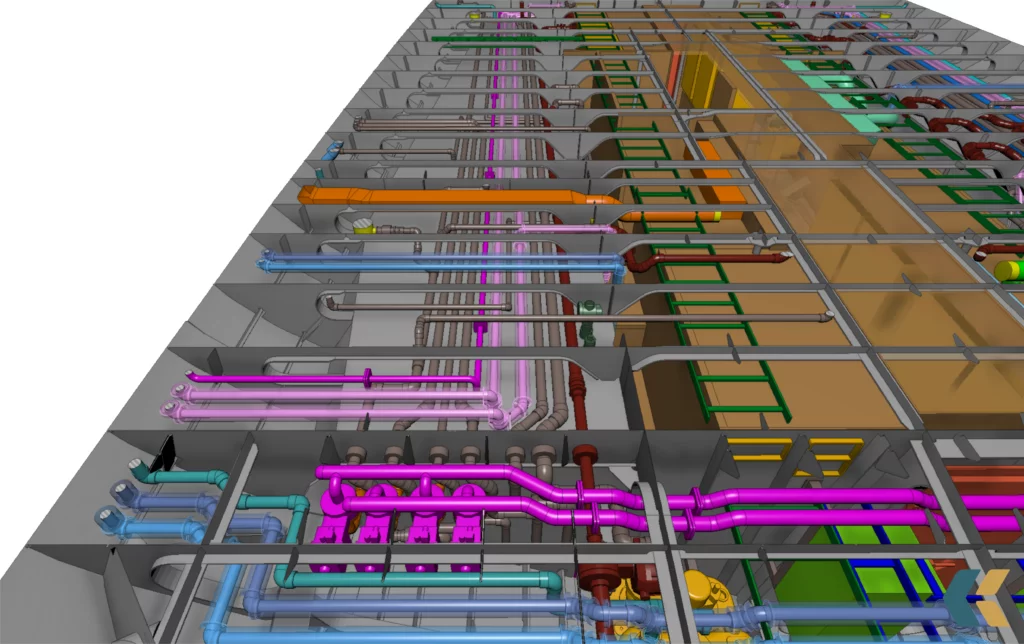
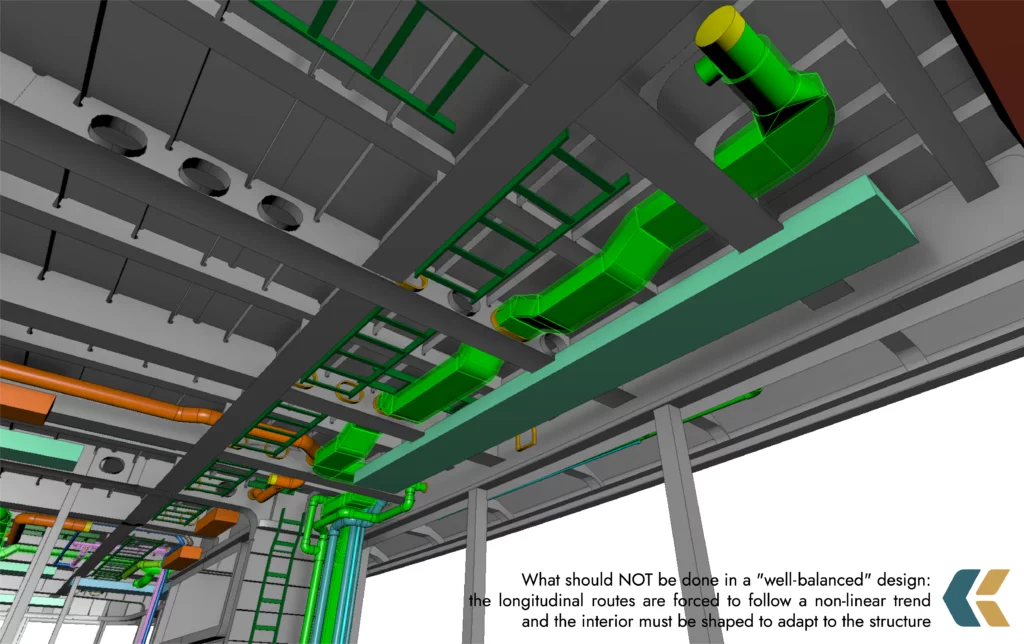
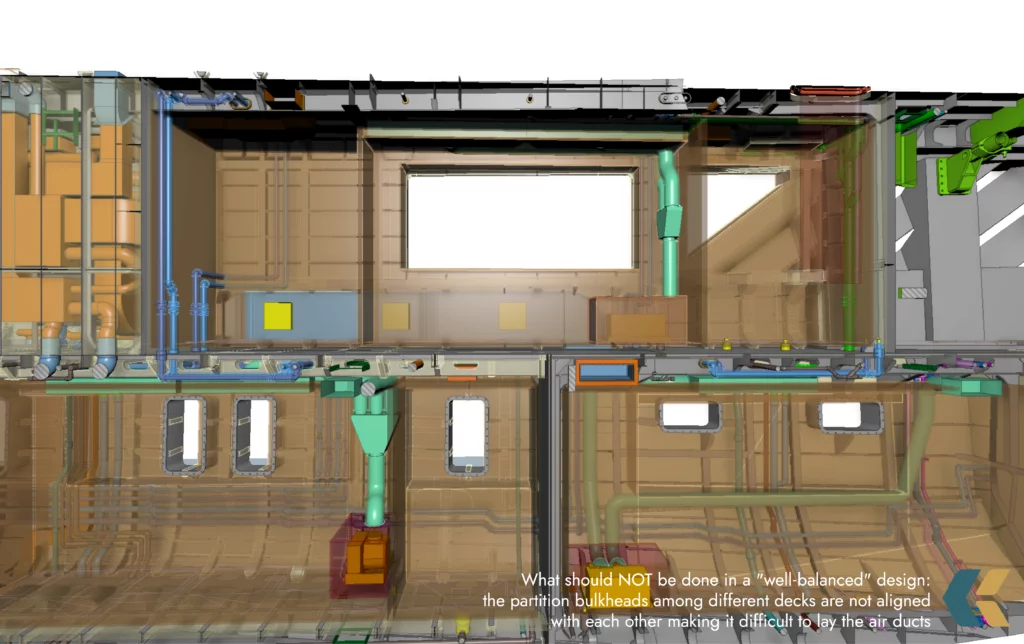
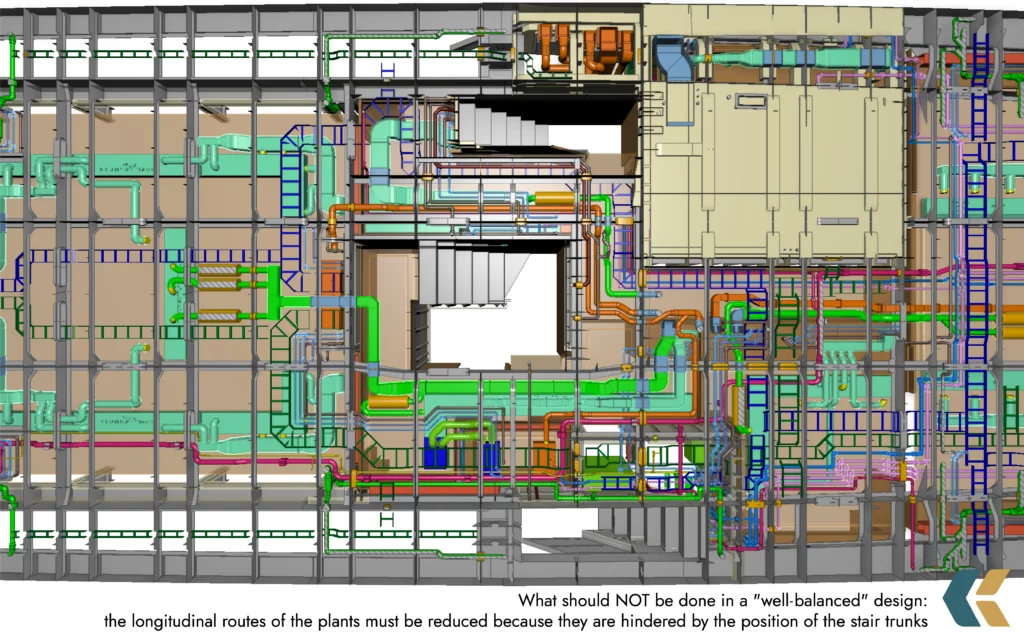
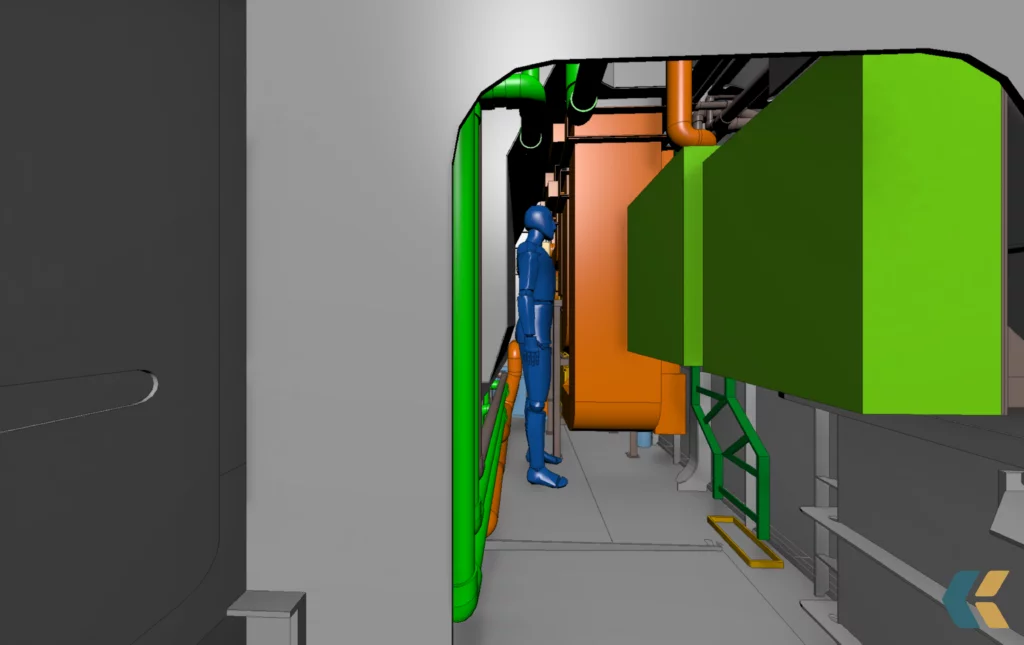
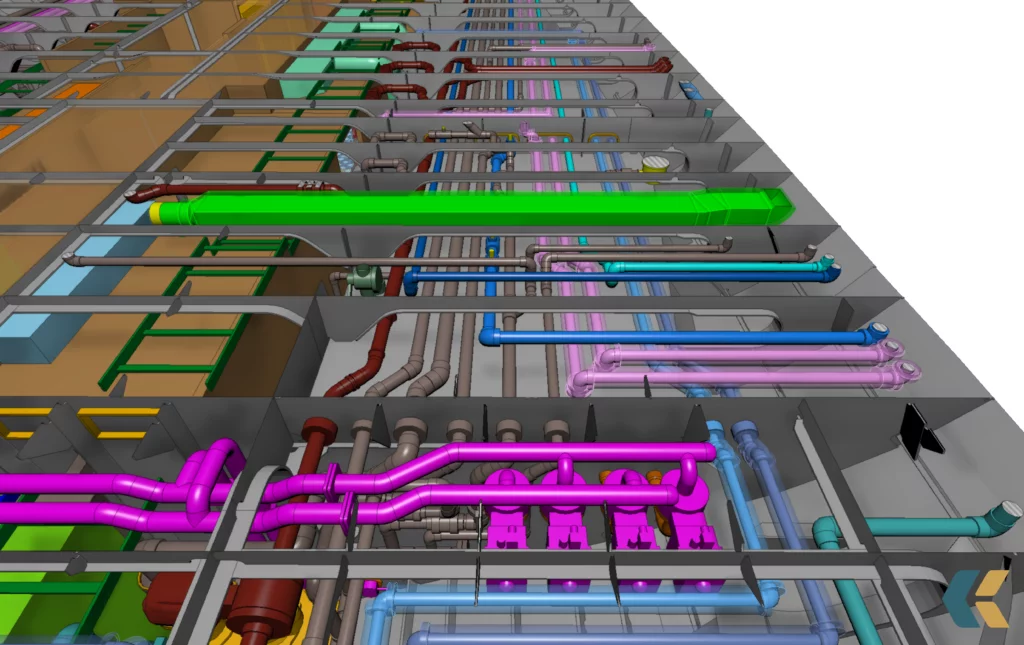
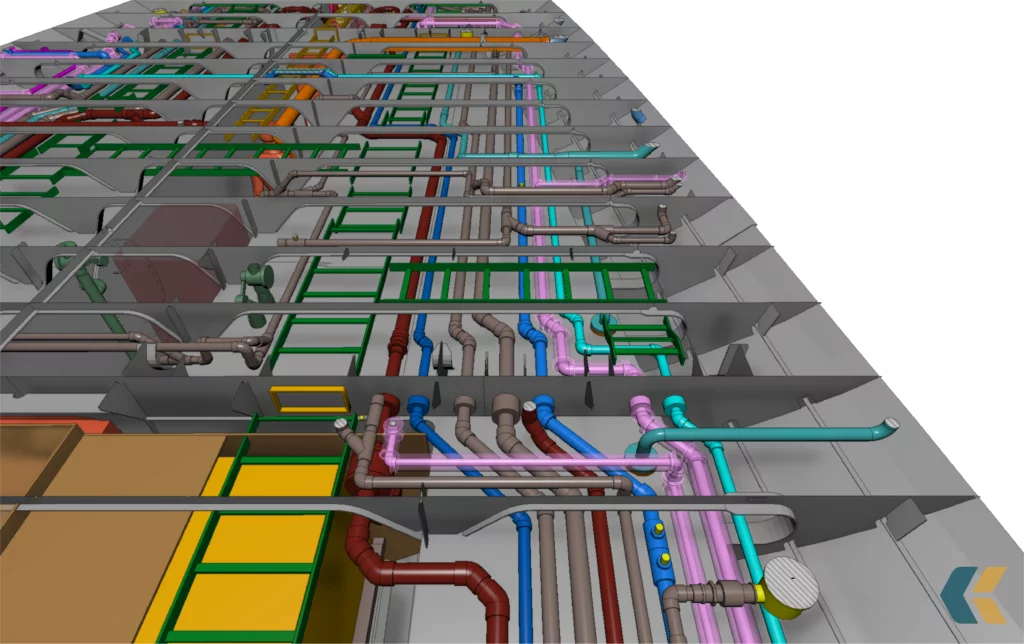
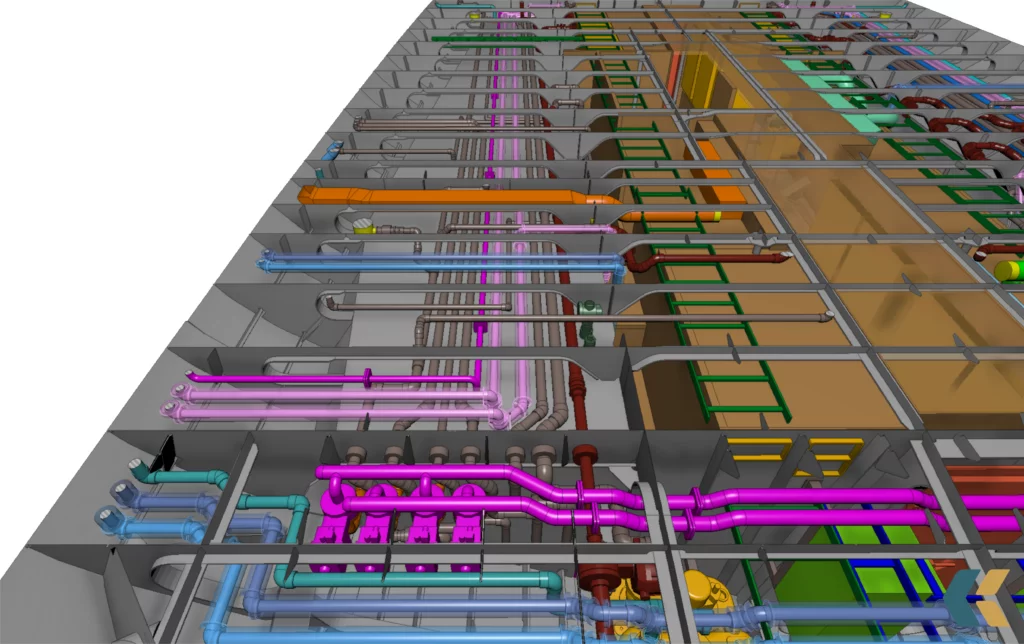
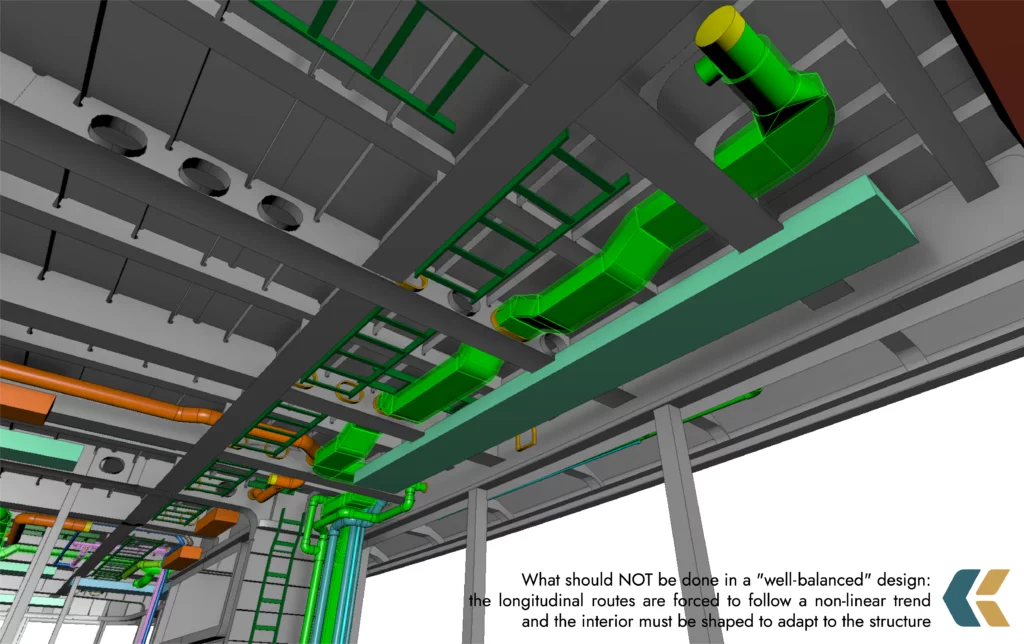
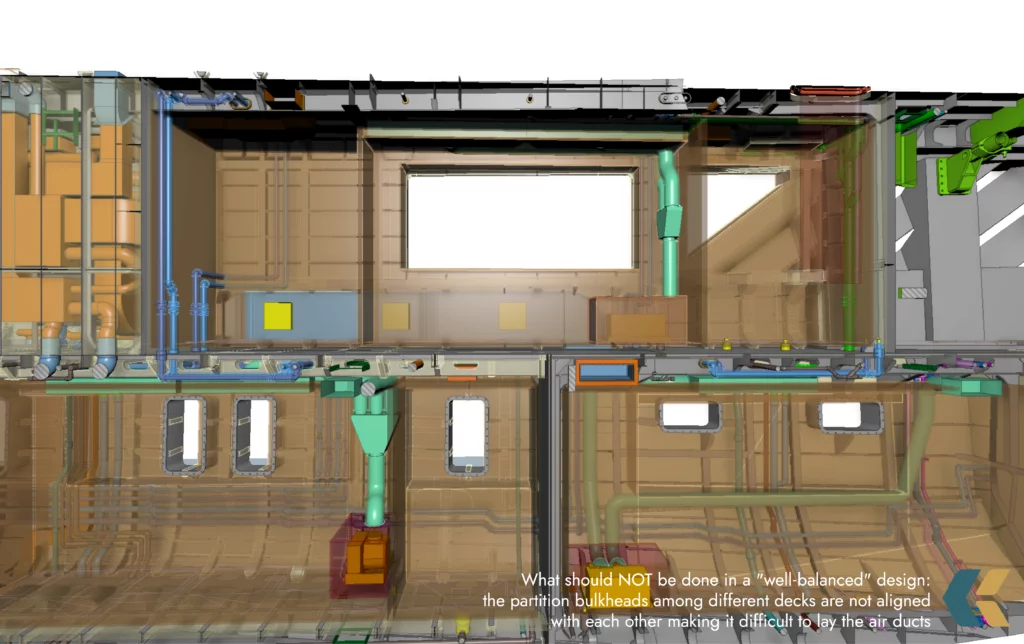
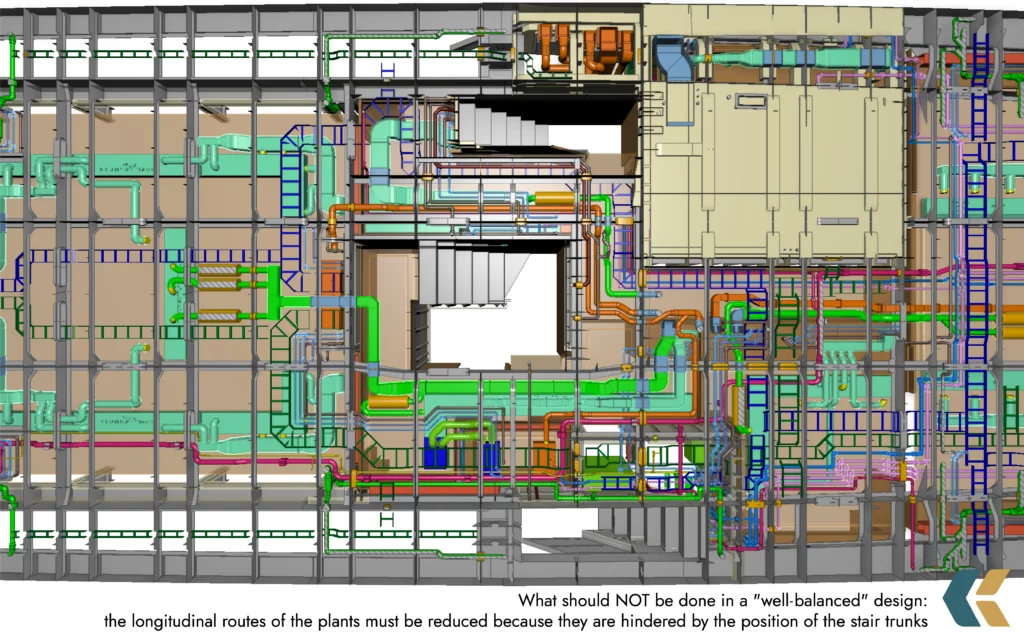